Glossary of Dyeing Techniques
Glossary of dyeing techniques
From indigo rainbows to the Merry Pranksters’ LSD-inspired invention of 1960s tie-dyes - dyeing yarns and cloths is ancient, experimental, and meaningful. In ancient Rome, Tyrian purple, produced by crushing thousands of sea snails, signified the elite class. (“Born in the purple” was an idiom for offspring born to a reigning emperor.) When the Romans went north to conquer Britain, they were repelled by celts dyed head to toe and tattooed in blue from the plant woad. Across the ocean, Mayan and Aztec elites wore a red color derived from a scale insect collected off cacti. Indigo blue derived from indigo plants has virtually always been the working class color, while cerulean blue derived from lapis lazuli is emblematic of French royalty. In the Industrial Era, keeping a white shirt clean was only possible for the aristocracy. Pink was considered a boys’ color until it switched genders because of successful admen in the early 50s.
Early photography paints a drab world in its salt crystal gray scale, but the world has always been as colorful as a field of poppies. With such a vast and ancient history, many techniques have been developed and there are enough dyeing terms to deserve its own dictionary. Leaving alone each pigment’s complicated chemical composition, discovery, and social application - there are about 100 ways to dye a garment in the modern wheelhouse.
This feature won’t be completely exhaustive, but it will answer every term commonly used in the fashion industry, plus a few obscure ones that we use (or have used) on our site. We’ll start alphabetically and end with a few extra notes on some related terms.
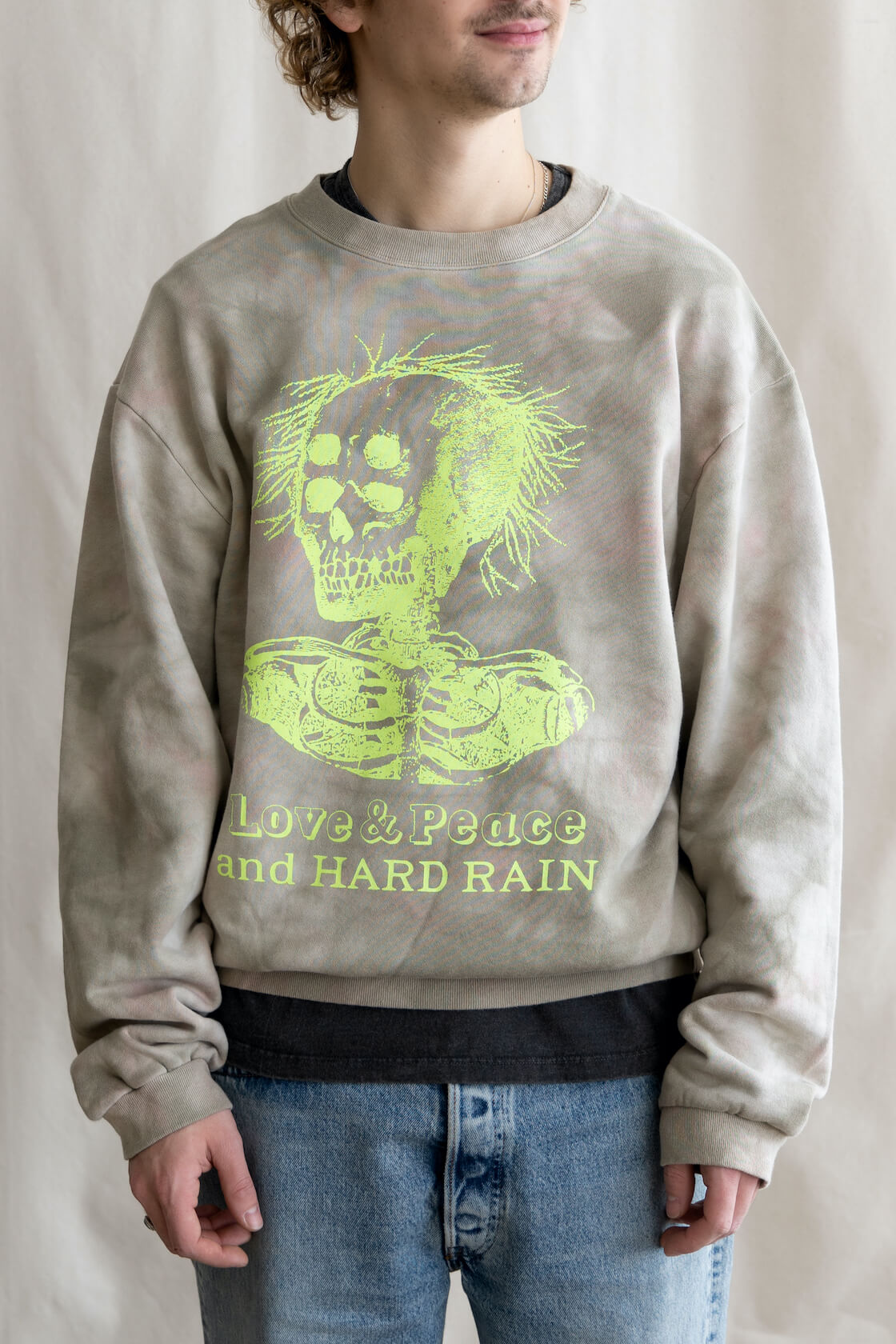
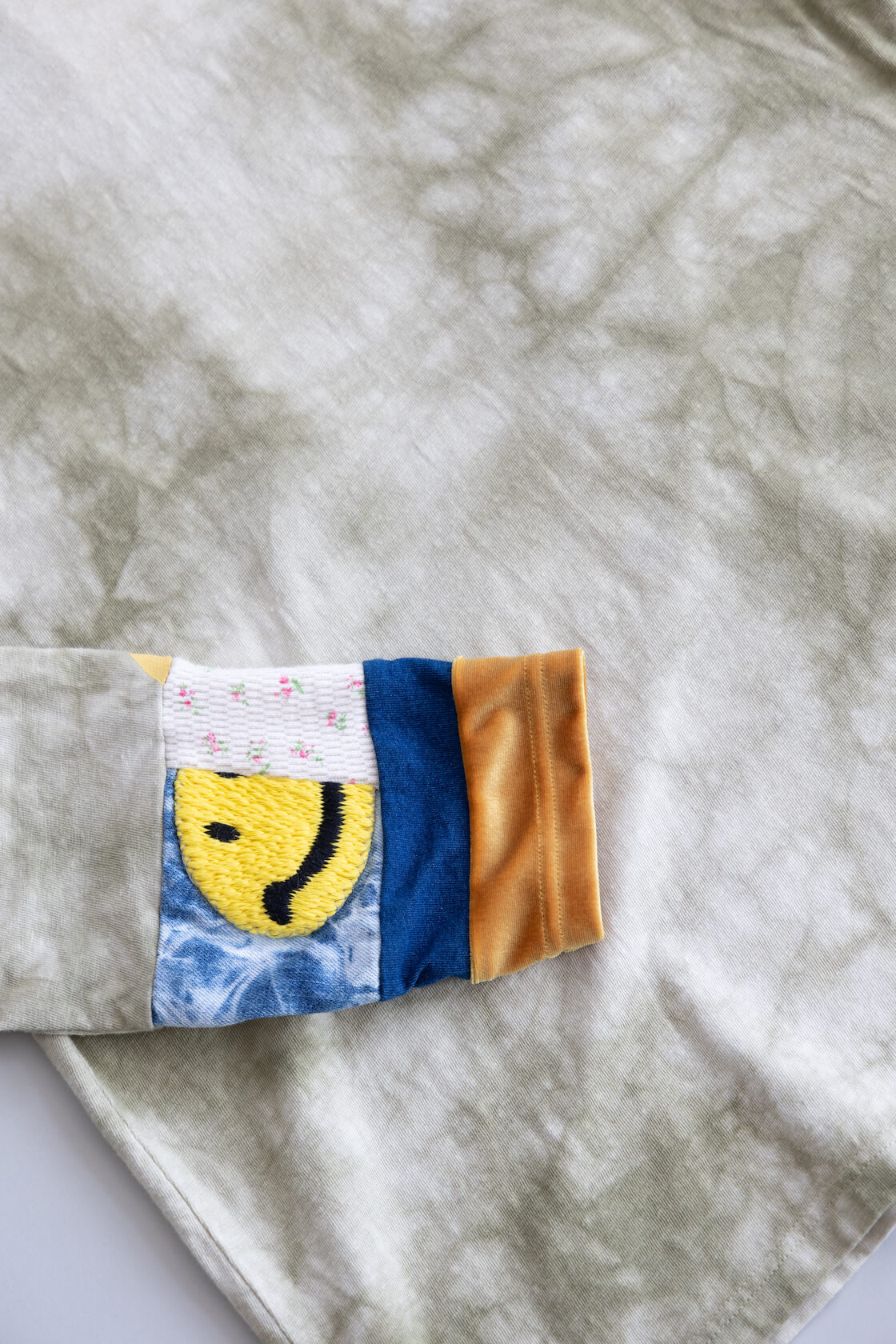
Ashbury Dyeing
This is a signature style that is unique to Kapital. Ashbury Dyeing is a technique similar to American tie-dyes popularized in 1960s California combined with the traditional Japanese tie-dye techniques of shibori. Mostly sticking to the natural, muddy tones of vegetable dyes and a monochromatic color scale, this is Kapital doing what Kapital does - combining cultural references and highlighting various disciplines of textile art.
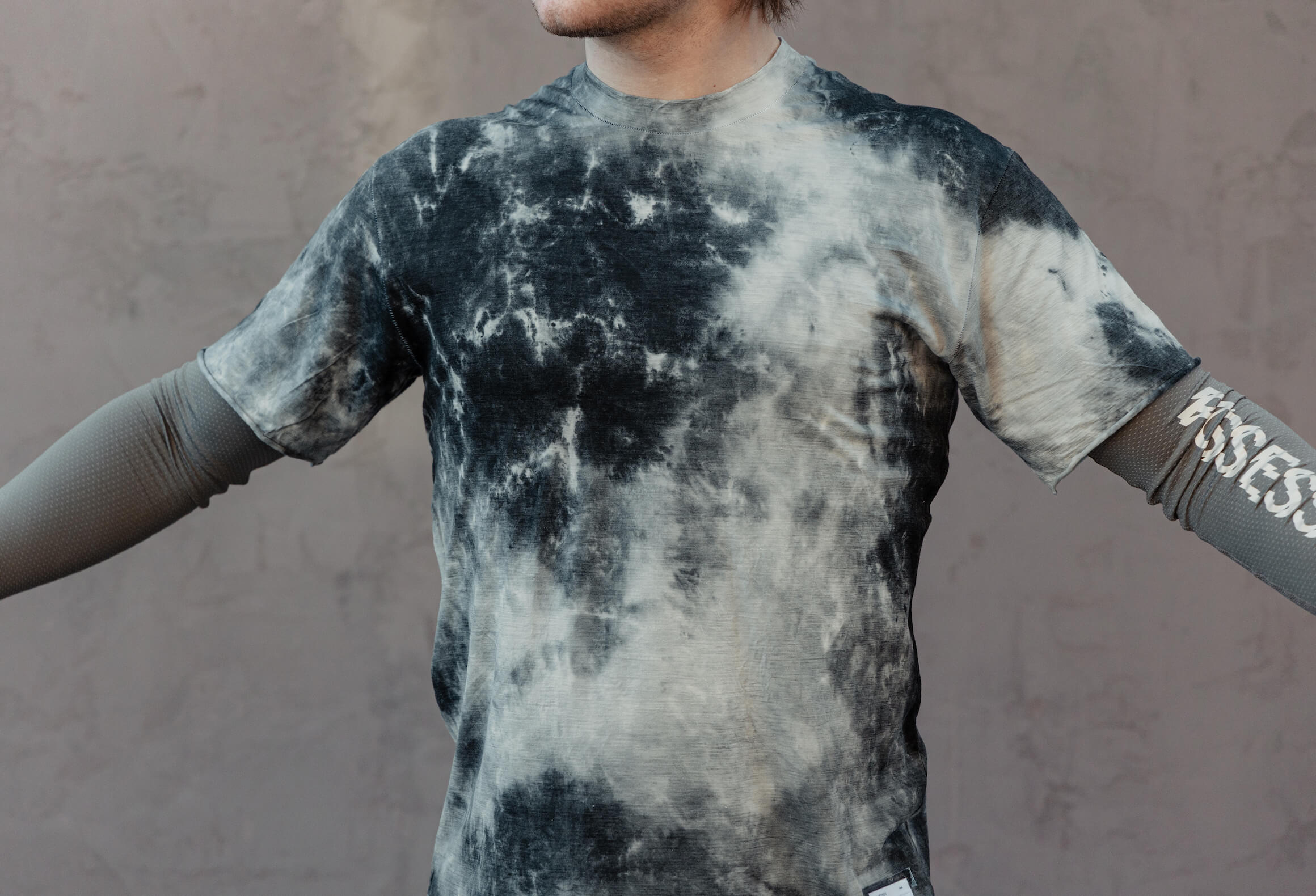
Discharge Dyeing/Printing
Discharge Dyeing or Discharge Printing is where a dyed garment is then printed with a pattern or design by applying a color destroying agent such as chlorine, bleach, or hydrosulfite. This creates a white or lighter color on a darker background like a photographic negative and is often used in conjunction with another dyeing technique like resist dyeing (ie. tie-dye, shibori).
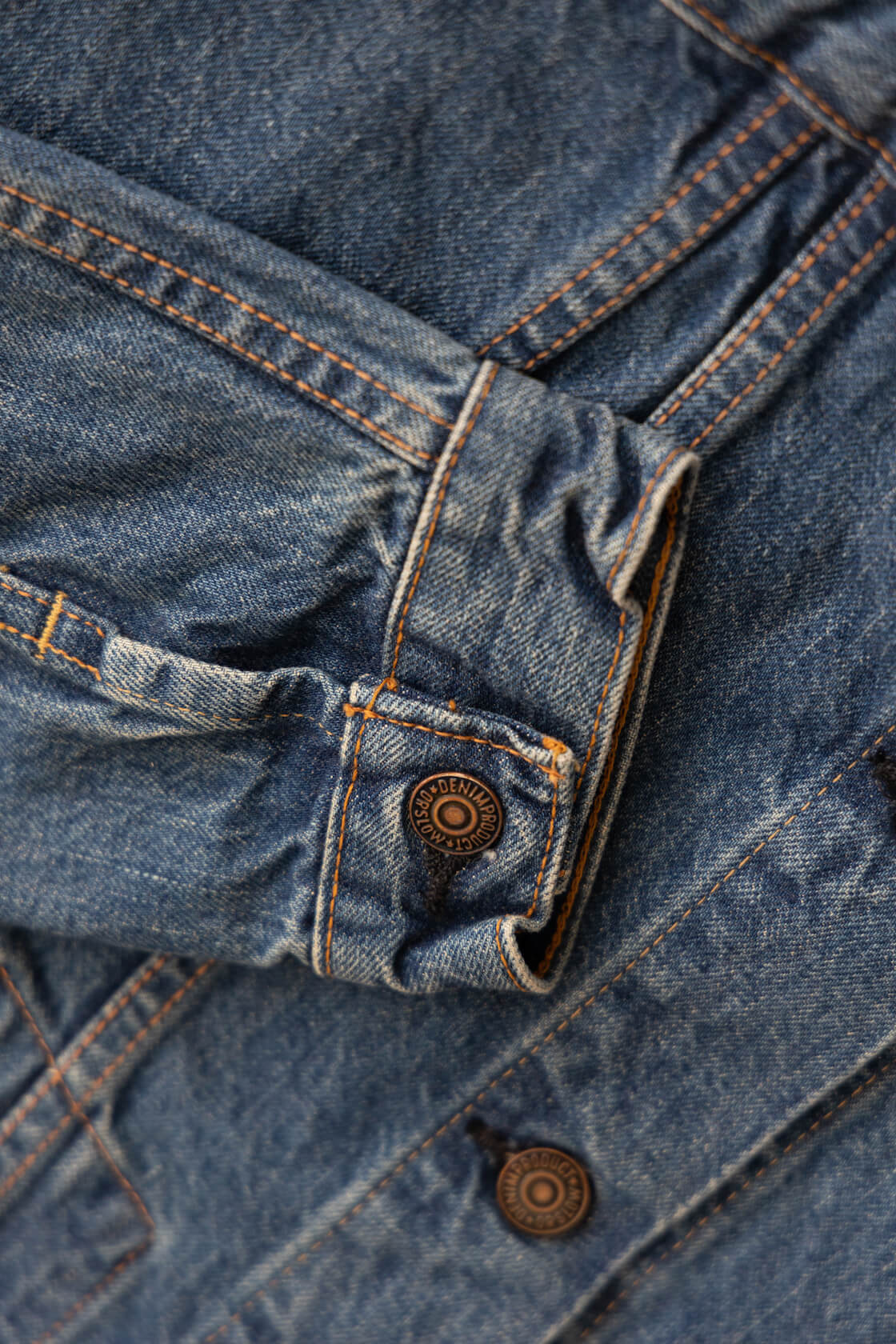
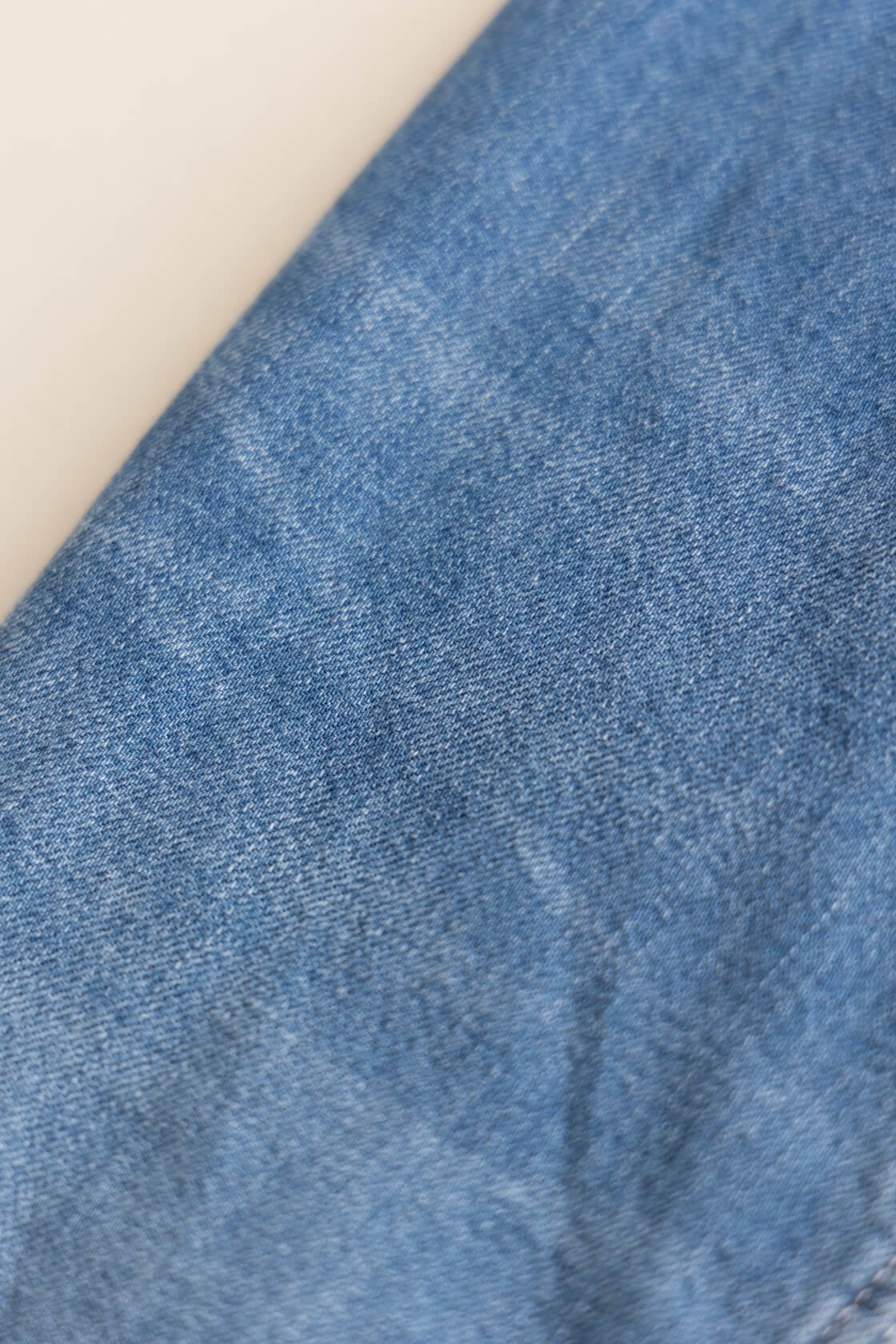
Direct Dyeing or Dyed in the Yarn
Most clothing is direct, or reactive dyed, meaning that the fabric is dyed prior to assembly. This can be done as a fiber (Stock dyeing) or Dyed In the Yarn. This allows designers to match a specific pantone every time for consistency. For garments dyed in the yarn, saturation depends on how long the yarns are held in the dye bath and determines eventual fading. This is common to every direct dyed garment, but is most popularly recognized in denim fades where traditional blue jeans begin to show the white core of the dyed yarns over time (further emphasized by the weft usually being left undyed in twill cotton denim).
Garment Dyeing or Pigment Dyeing
Garment dyeing, also known as pigment dyeing, creates beautiful fading. Garment dyeing is an overlay process where undyed, assembled clothing is left in a dye bath, dried, removed, and then often put back into the dye bath until the intended color depth emerges. It is often used for pastels (as darker colors require repeated dye baths). Garment dyeing gives clothing a softer hand and vintage appearance with the seams and thicker areas developing rich tonal gradation. (This also happens in Direct Dyed garments, but only after wash and wear.) Because Garment Dyed garments are most commonly produced in small batches, individual color variation between garments of the same pattern occurs.
Overdyeing
Overdyeing is either leaving a garment for an extended period in the dye bath or dyeing a garment more than once in order to attain deeper colors. Sometimes used interchangeably with garment dyeing, "overdyeing" is more often used to indicate that an additional dye process has been added to a direct dyed garment.
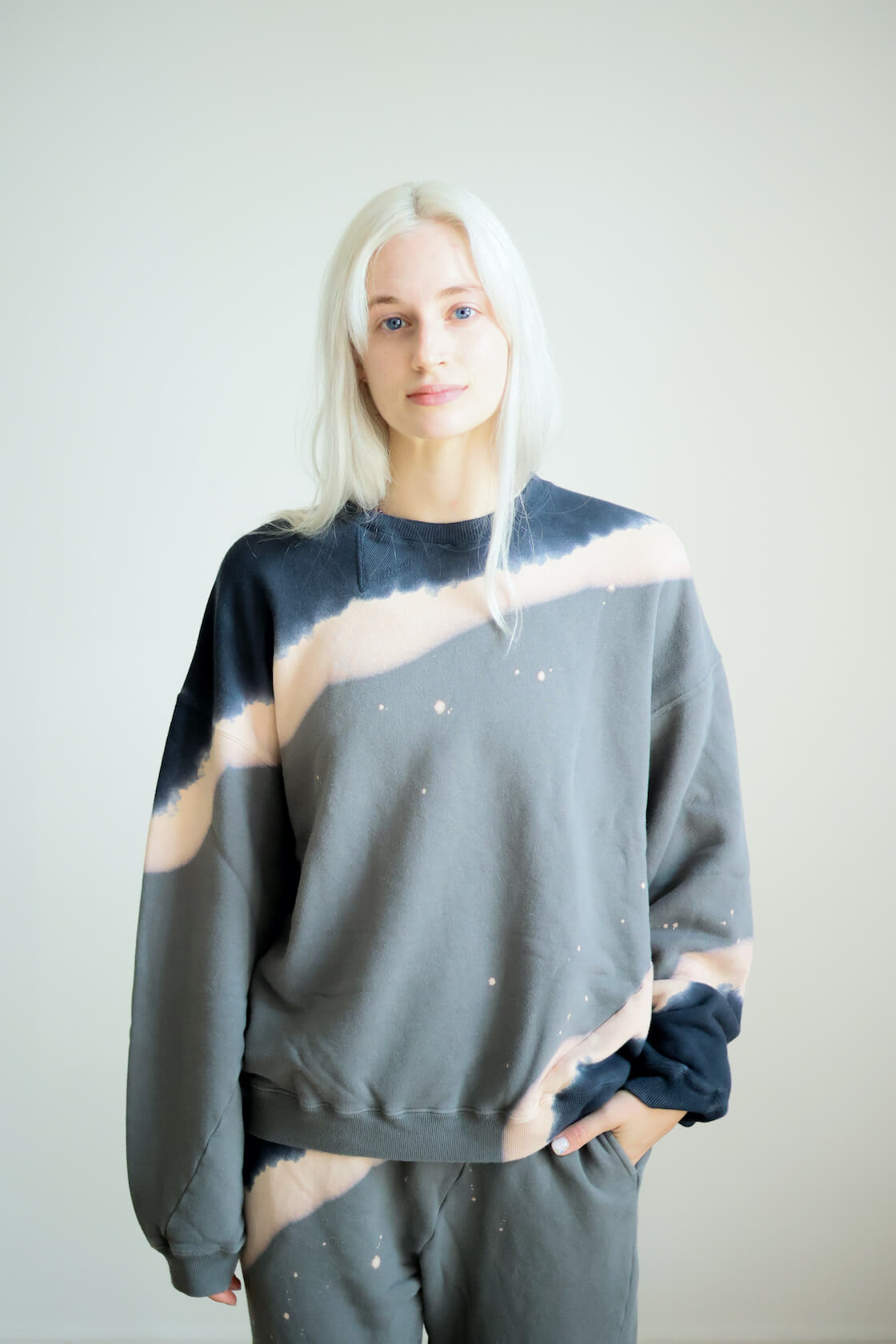
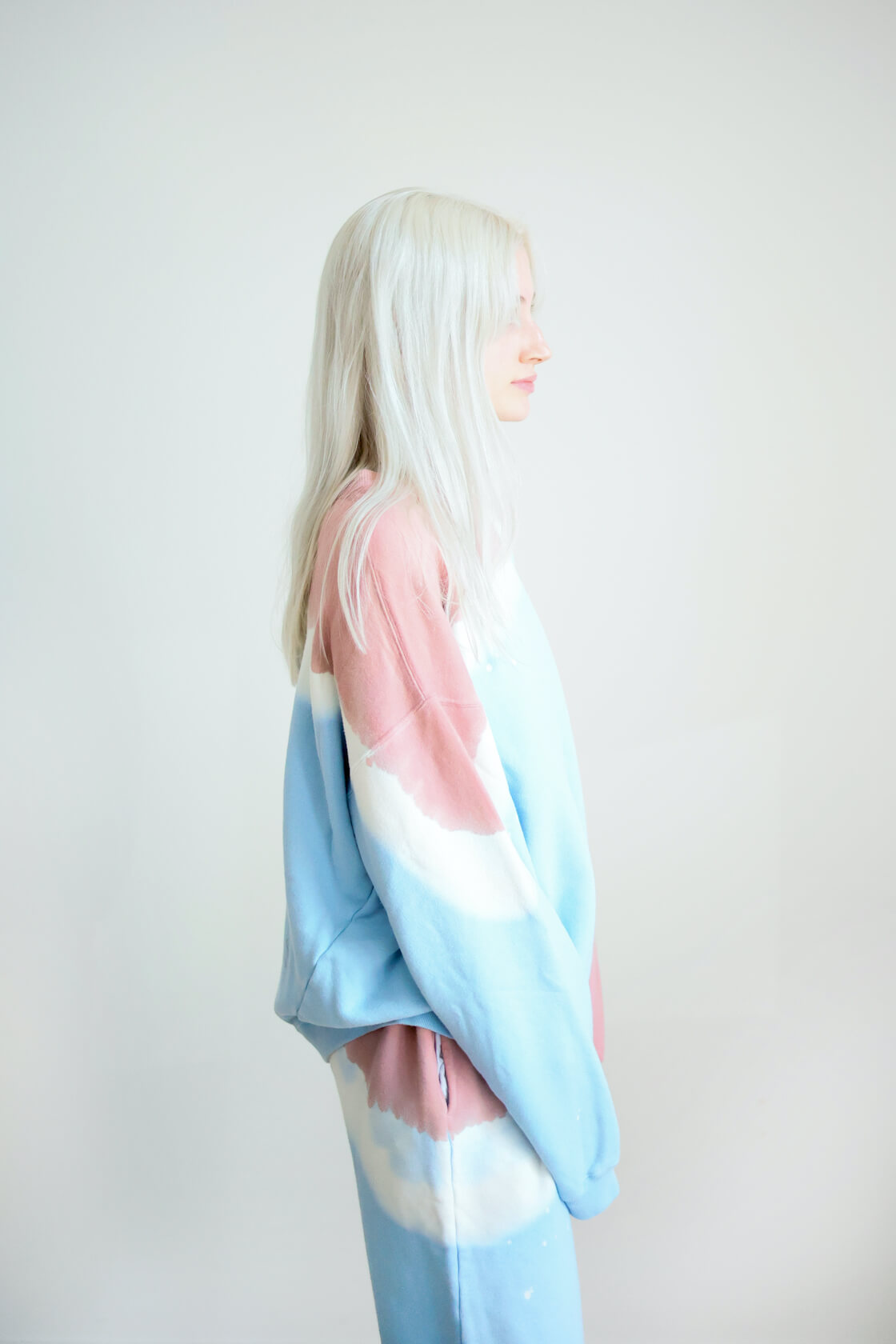
Resist Dyeing
Resist dyeing is a method of dyeing textiles with patterns. Methods are used to resist the dye from reaching all the cloth. The most common resists are wax (as in batik), tying (as in tie-dyes), or a combination of tying and stitching [as in shibori (discussed below)].
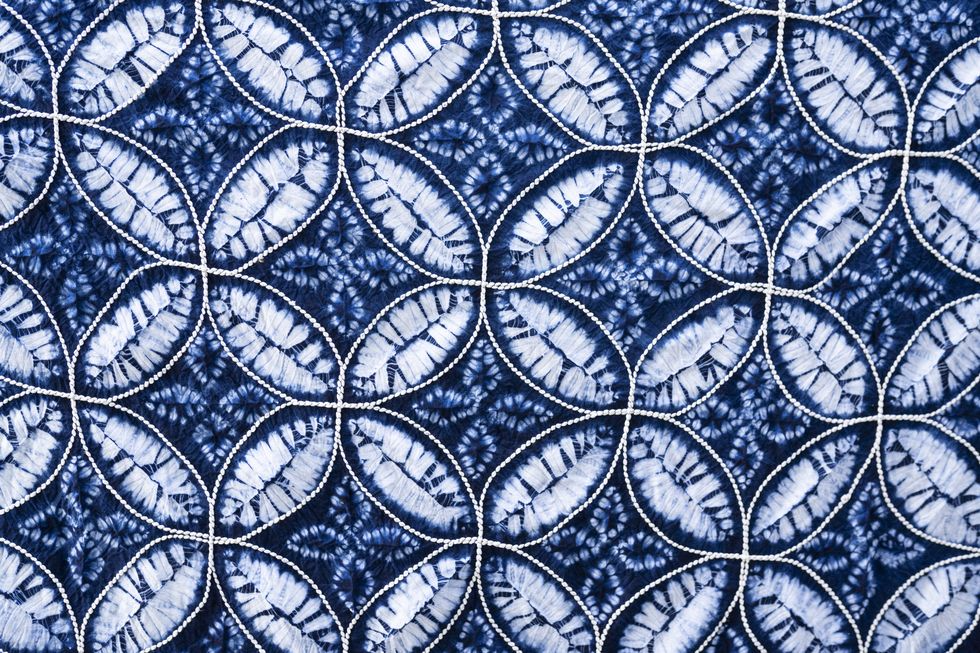
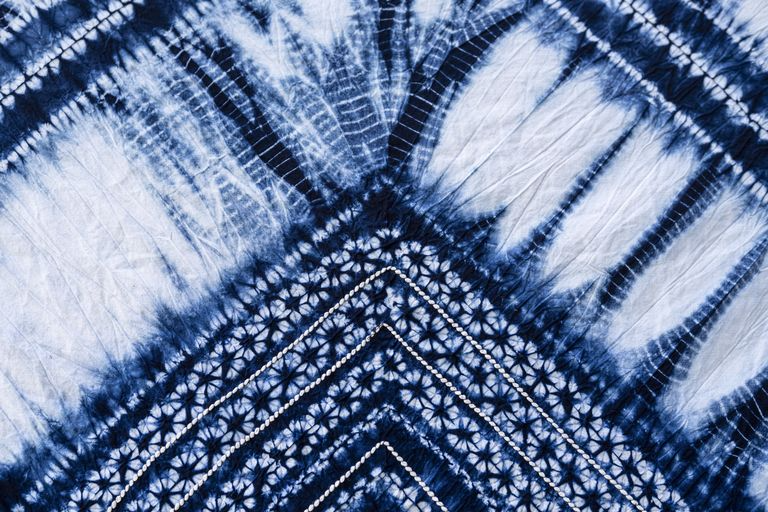
Shibori Tie-Dyeing
This one deserves a little longer of an entry because of its long tradition and complicated processes. It isn’t common to see in fashion, but a few brands we hold (Kapital, Kiriko, Anonymous Ism) have used this process in their design to awesome effect.
Shibori is a Japanese manual resist dyeing technique of tie-dyeing. The earliest known example dates from 8th century Japan found amongst gifts given by the Emperor Shōmu to one of the Buddhist Seven Great Temples in the city of Nara. Shibori includes various resist techniques that include stitching elaborate patterns and tightly gathering the stitching prior to dyeing that become far more intricate, detailed, and feature more controlled patterns than western tie-dyes. Shibori tie-dyes also tend to be monochromatic. There are six different traditional techniques used in shibori.
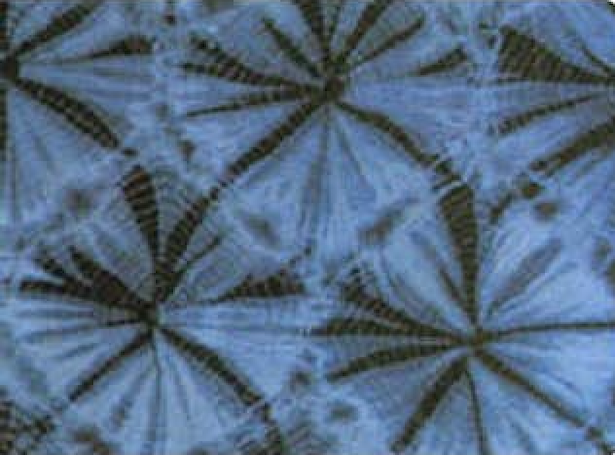
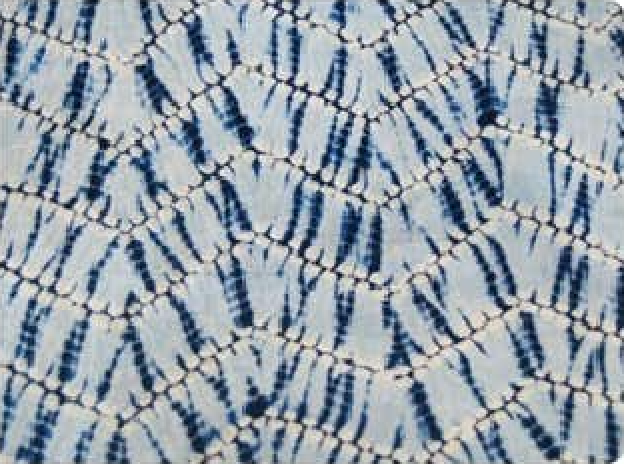
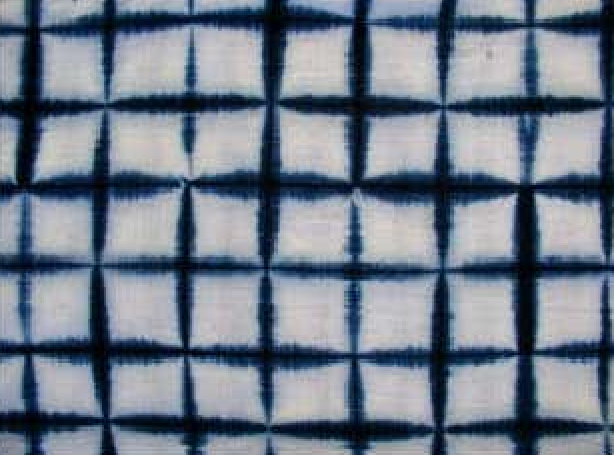
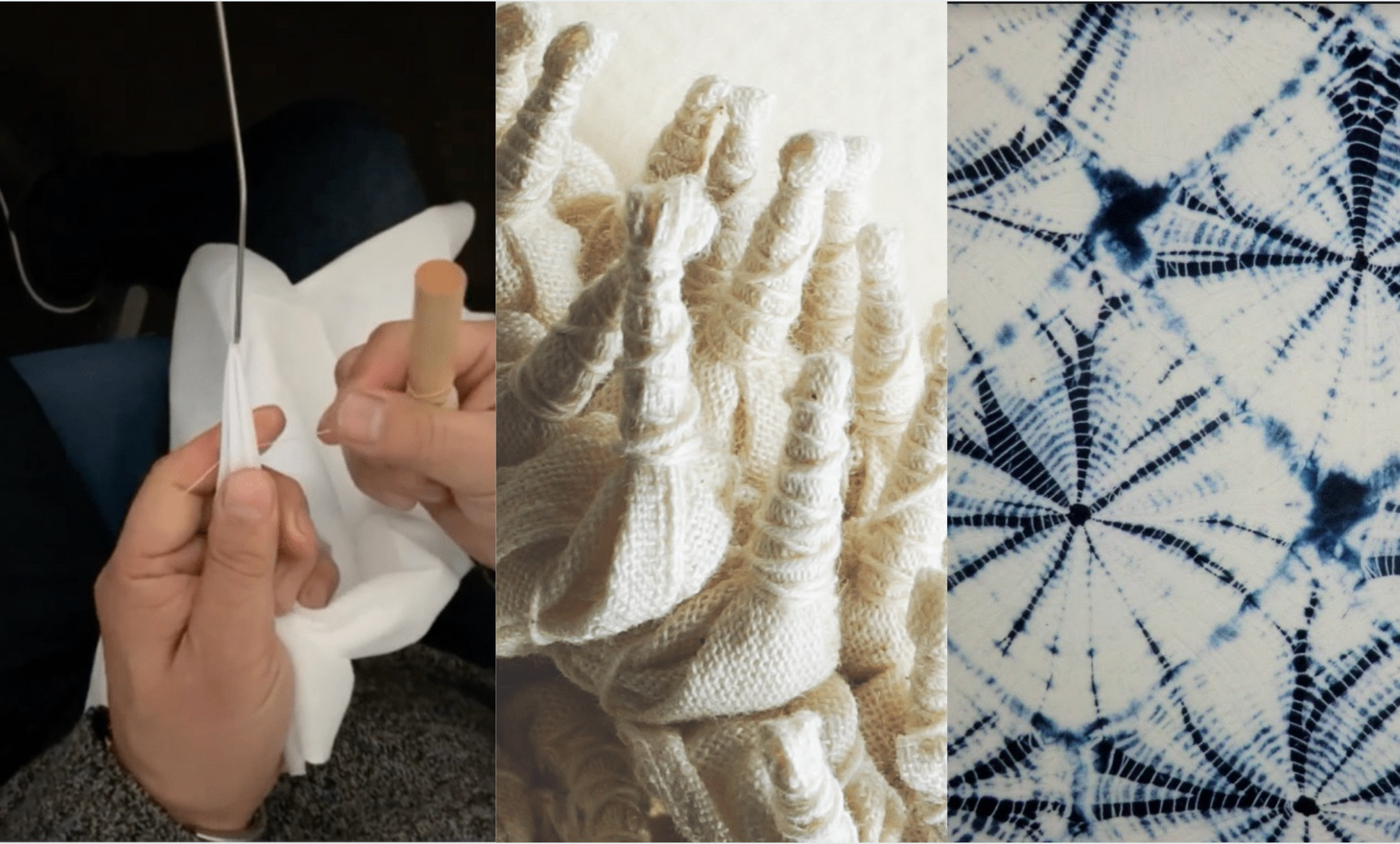
Kumo Shibori
This technique involves gathering, pleating and binding the cloth. This method is mostly used to create spider web patterns similar to western tie-dyes.
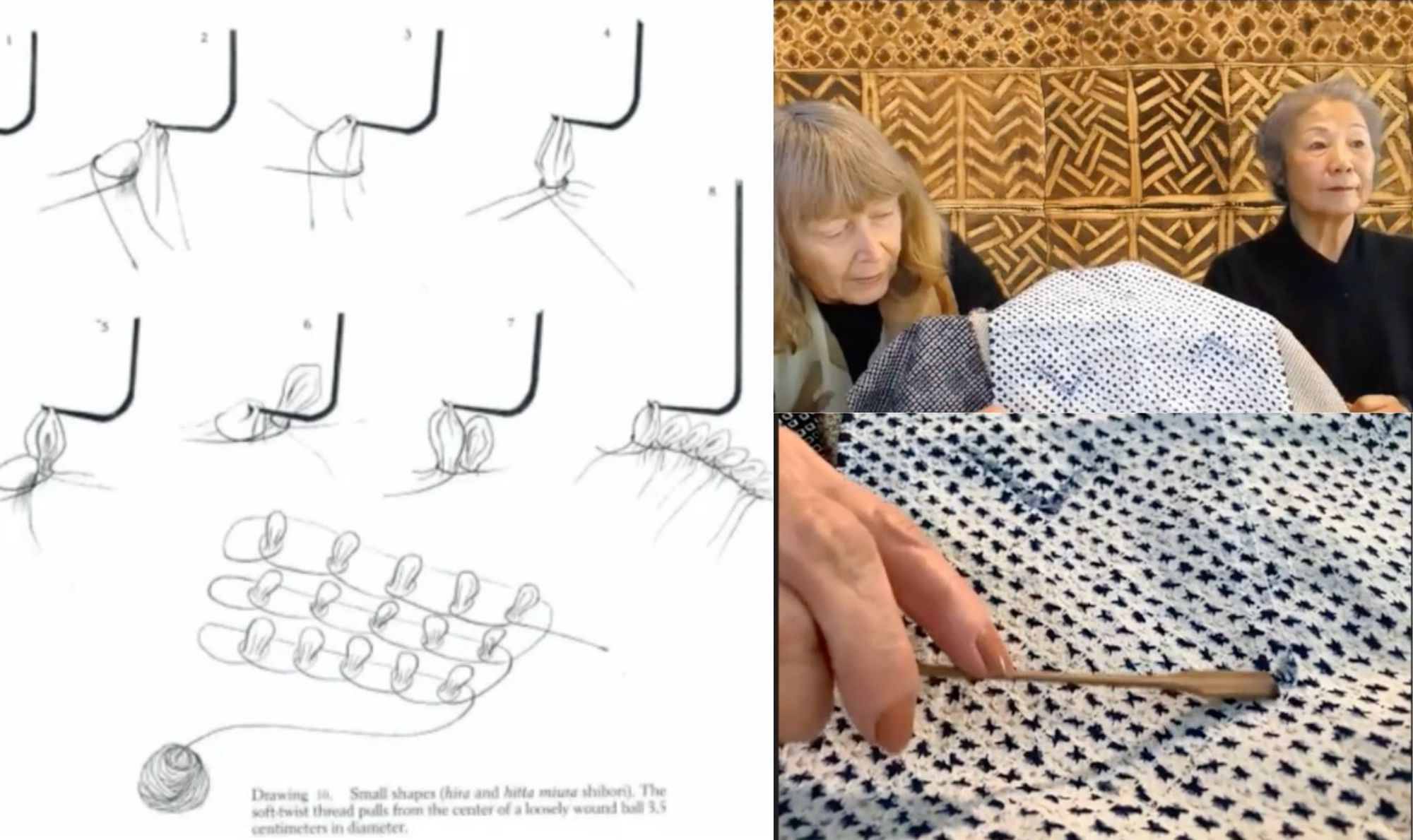
Yoshiko Iwamoto Wada (Pictured at far right) is the author of Shibori: The Inventive Art of Japanese Shaped Resist Dyeing - considered the definitive classic on the subject since its publication in 1983.
Miura Shibori
Miura Shibori uses the processes of looping and binding to create patterns. A slightly more involved process, miura designers pluck pieces of the cloth with a hook and needle and wrap it with thread. The outcome is intricate repeated patterns.
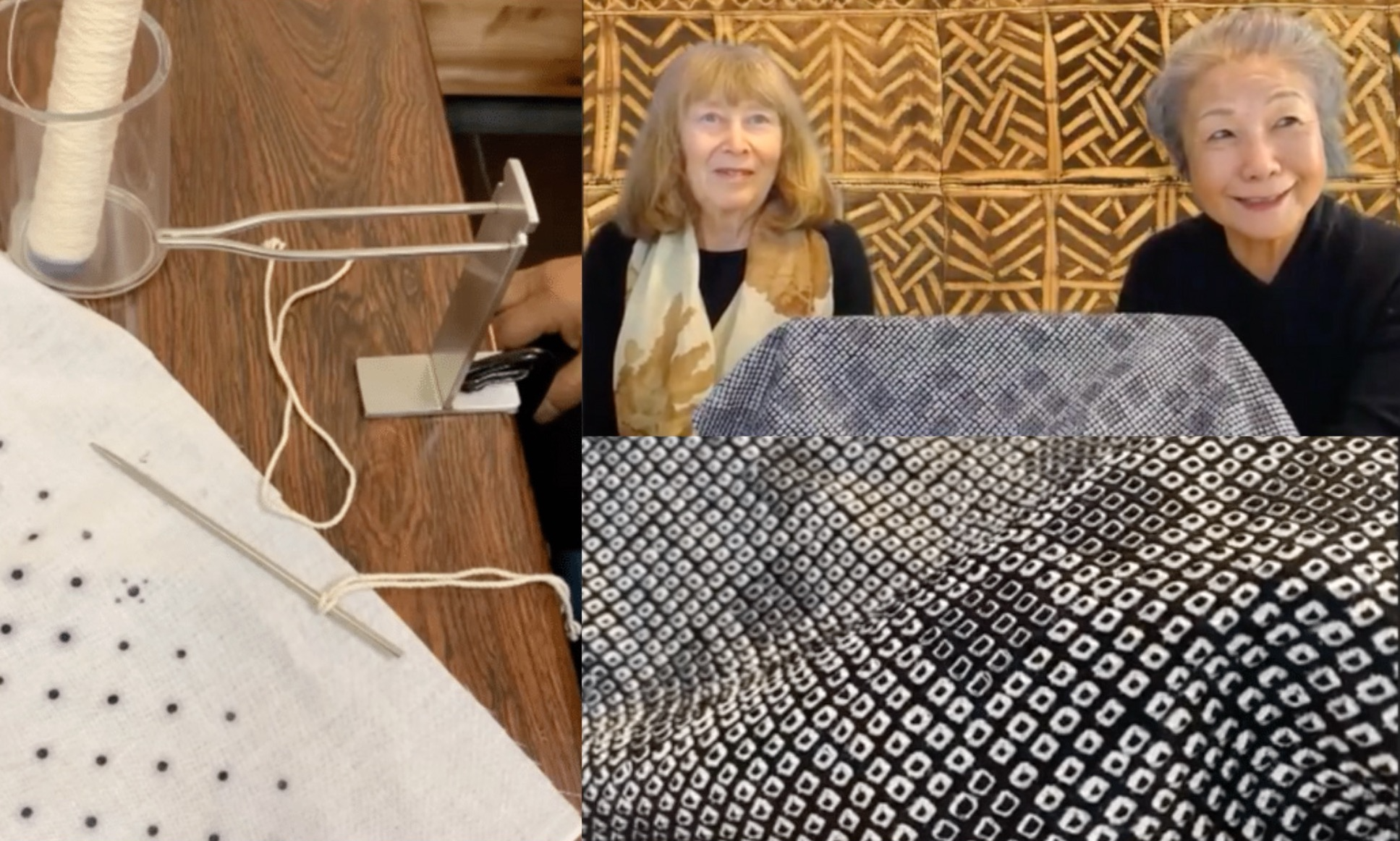
Kanoko Shibori
Kanoko Shibori evokes the spotted baby deer, called ‘fawn dots’ and favored by ladies in Imperial Court during the Heian Period (794-1185). Originally produced in Kyoto by skilled artisans, Kanoko Shibori were luxury items that became subject to sumptuary laws to restrain extravagance.
This method involves binding small, pinched sections of the cloth to create circular patterns. Each thread is hand tied, resulting in a semi-uniform appearance that upon scrutiny has intricate variations within each shape. Different tensions and tying locations can be used to create different patterns, and folding the fabric can also be incorporated into this process before binding.
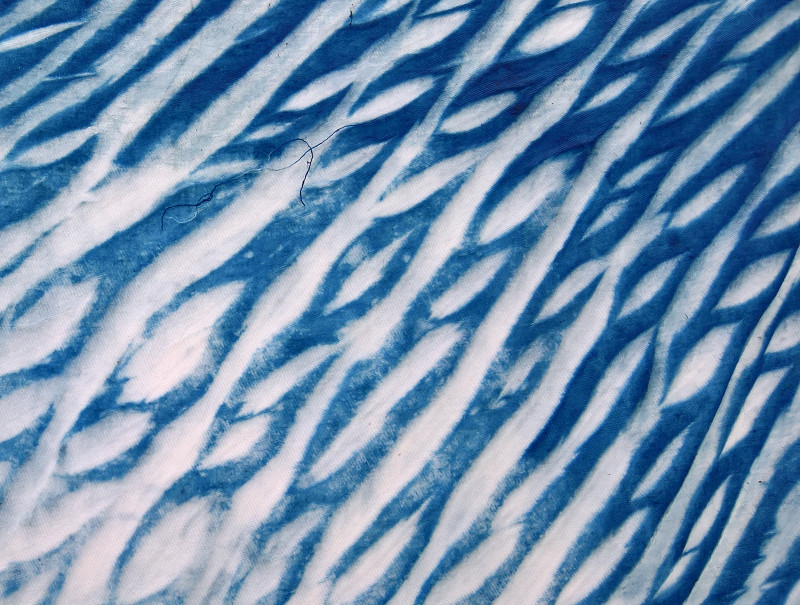
Arashi Shibori
Also referred to as pole wrapping shibori, arashi utilizes wooden or copper poles to twist, wrap and then bind the cloth with thread before dyeing. Arashi is the Japanese word for “storm” and the resulting patterns are made up of irregular diagonal lines that are meant to resemble heavy winds or stormy seas.
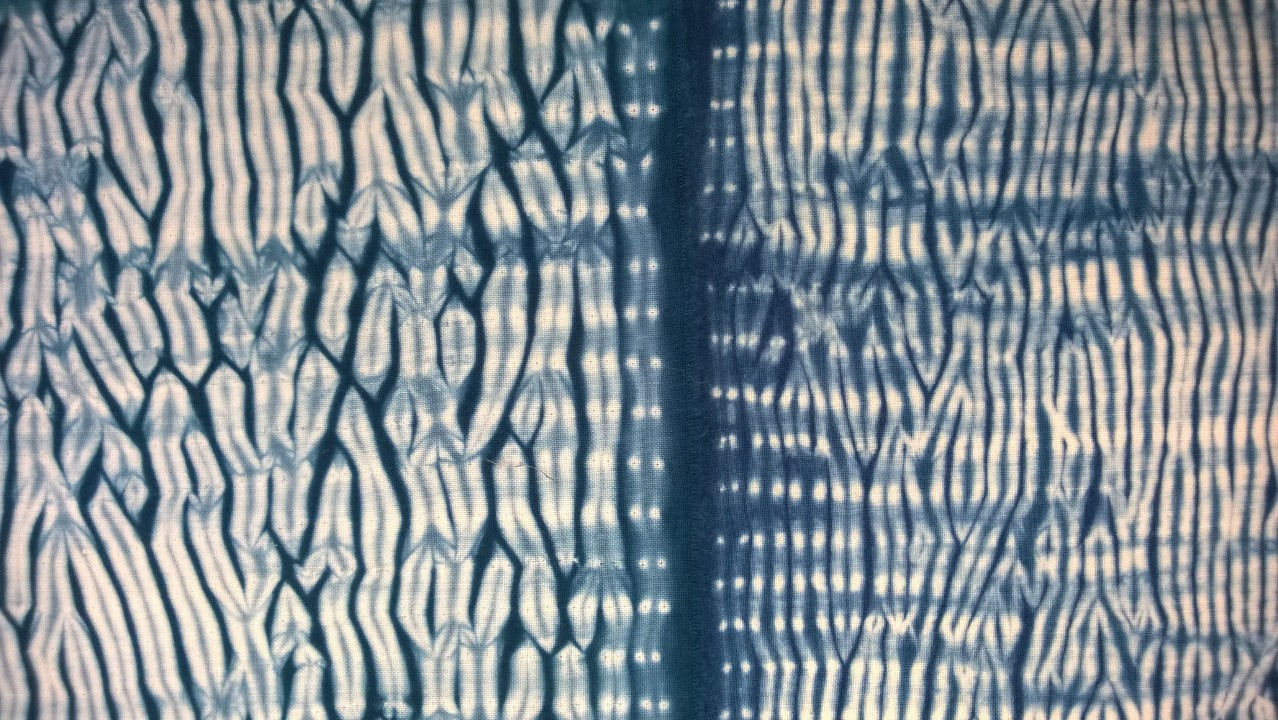
Nui Shibori
Nui Shibori is a stitching technique used to create more accurate and precise patterns in shibori dyeing. A simple running stitch is commonly used and sewn evenly in a constant forward movement and then pulled tight to gather sections of the fabric. Wooden dowels are sometimes used to help tighten the treads as much as possible. Stitching affords flexibility and control to create designs of great variety - delicate or bold, simple or complex, pictorial or abstract. Each end of the thread is then tied before dyeing, leaving channels of dyed and undyed cloth.
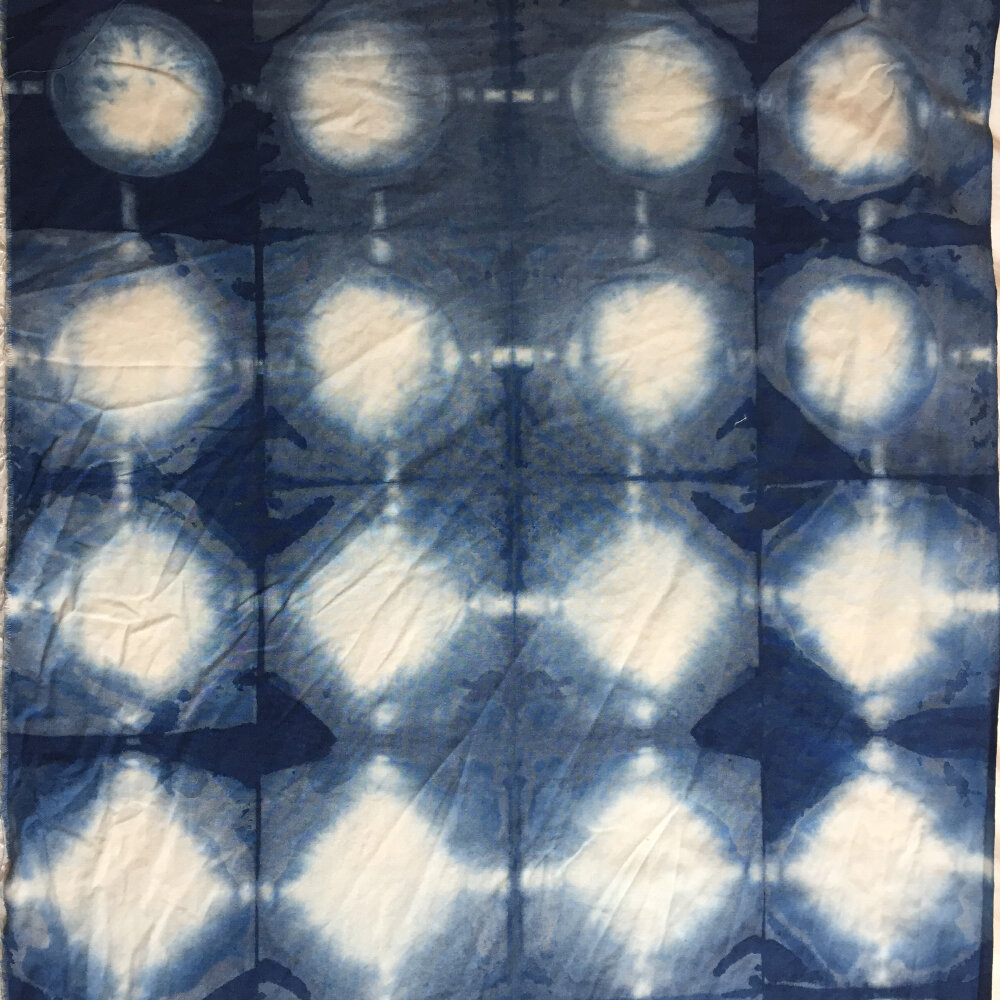
Itajime Shibori
Itajime Shibori is achieved by folding cloth and sandwiching it between two pieces of wood before dyeing. This shaped-resist shibori technique allows the dye to only penetrate the edges of the folded cloth, leaving contrasting un-dyed sections.
For more examples of shibori, check out the World Shibori Network.
Stock Dyeing
Stock Dyeing, also known as Fiber Dyeing, is when fiber staples are dyed before they are spun into yarns. This produces the highest level of color saturation of any dye process for natural fibers with very limited fading from wash and wear. Click here to see a video of the process and to better appreciate the scale of such an operation.
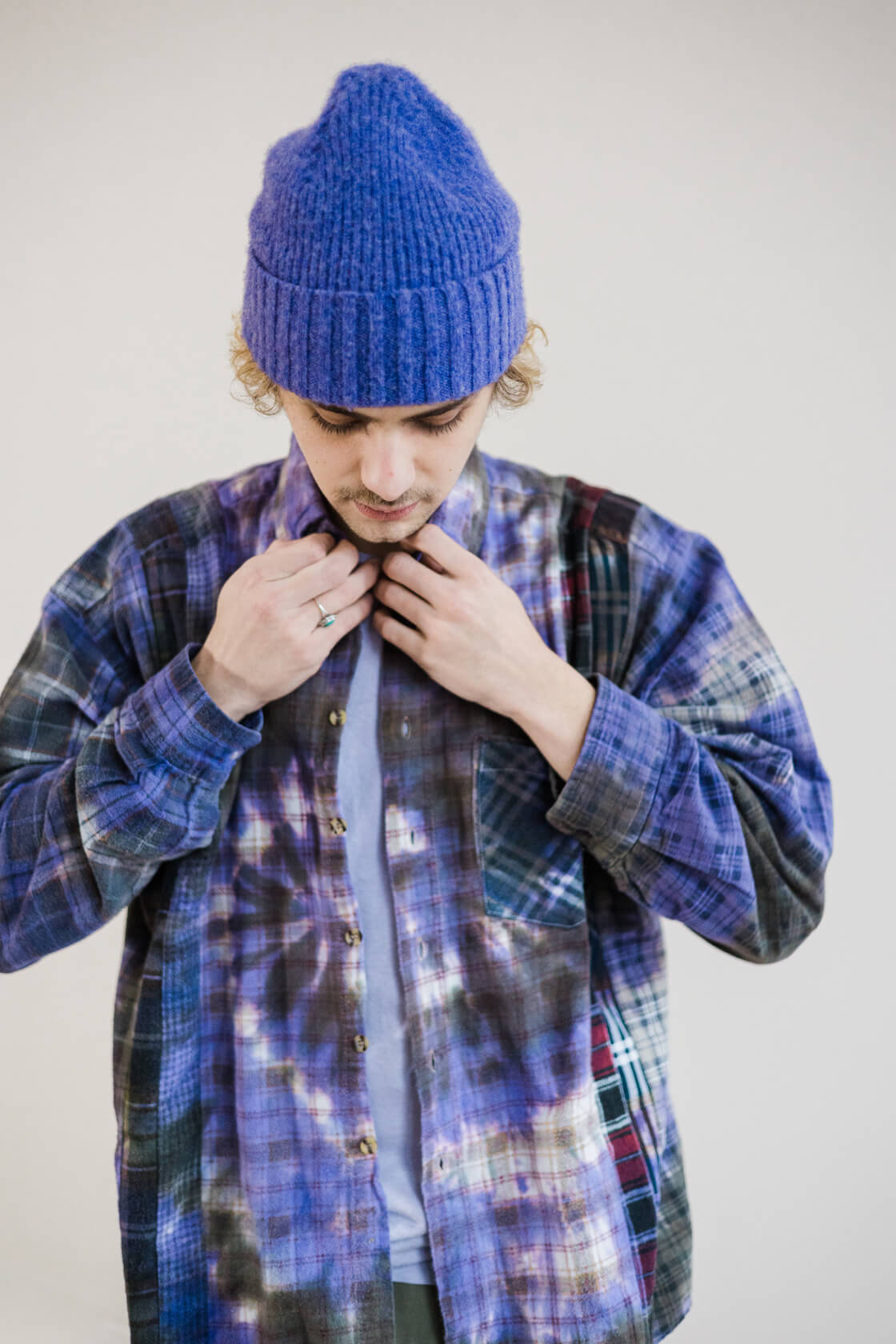
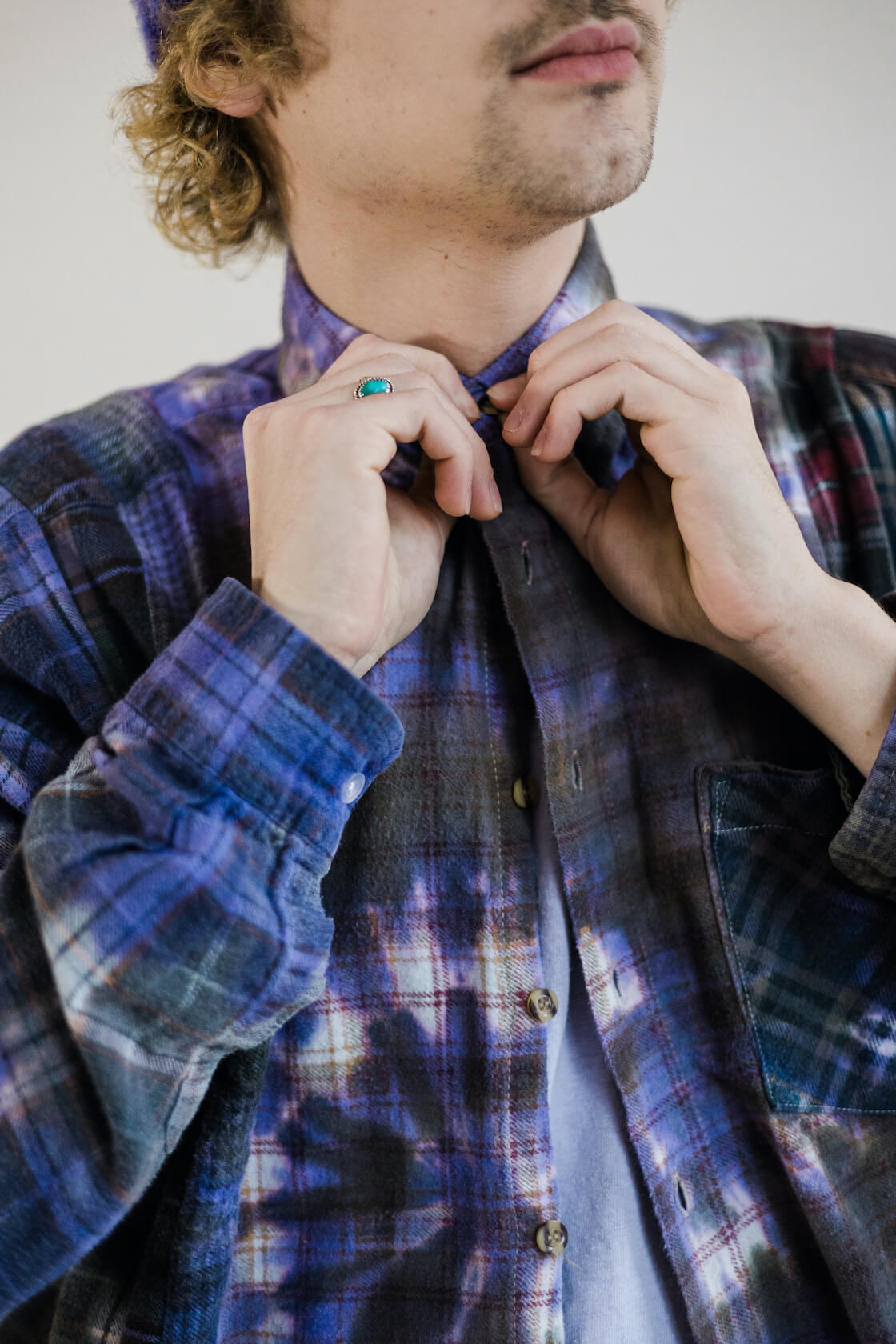
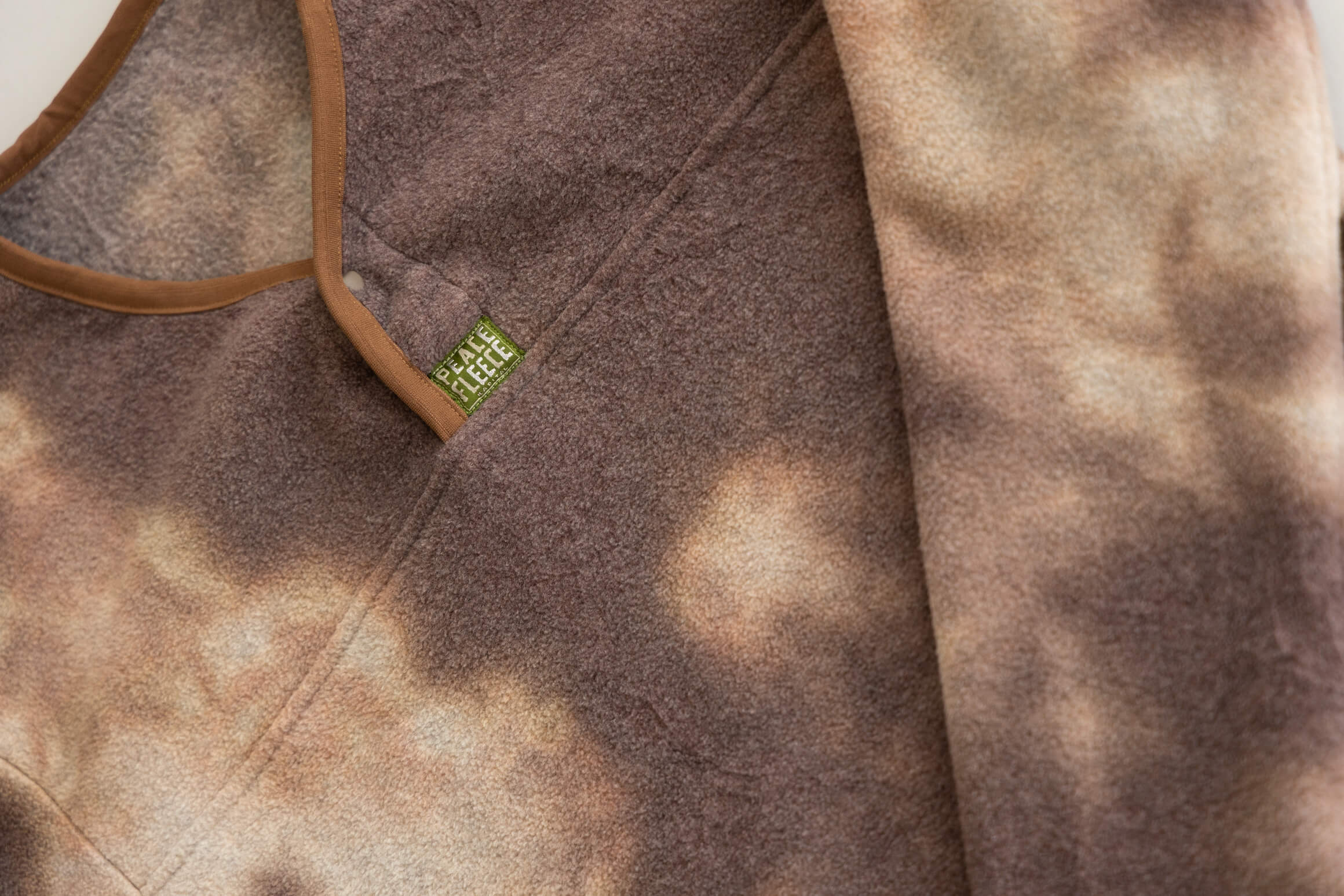
Tie-Dyeing
The iconoclastic peace activists Ken Kesey and his Merry Pranksters claimed to have invented tie-dye in 1964 by taking LSD beside a pond and pouring enamel-based model airplane paint into it before placing a white tee on the surface of the water. The swirling patterns were later copied by resist dyeing techniques and disseminated through psychedelic music and hippie culture. Tie-dyes are an American artform characterized by multiple bright colors in random patterns.
Other terms of Note
Colorfast
Colorfast, or color fastness, is a term used to describe dyes that won’t run when washed and have minimal fading over time. The term was first coined in 1916 by manufacturers of textiles in testing fabrics when exposed to light, washing, perspiration, and abrasion. The use of which is governed by the American Association of Textile Chemists and Colorists under specified standards of fabric and dye behavior testing.
The first dye that was considered “colorfast” is Turkey Red. Creating the dyestuffs was a complex and laborious process involving madder root and alizarin to fix the dye, as well as sheep’s dung, bull’s blood and urine. This odd combination produced a vibrant red that became one of the two standard colors for bandannas. As proof of quality, the words “color fast” or “fast color” began appearing on bandanas in the 20s. Turkey Red (as a process) was replaced by synthetic dyes in the early 20th century due to its laborious process and environmental impact. When you see “colorfast” on modern bandannas, that is more of a design homage to vintage bandannas than a quality statement. Nearly all bandannas use colorfast dyes today.
Additionally, outside of raw denim and indigo enthusiasts like Pure Blue Japan, most garments today are colorfast.
Vegetable Dye
Vegetable dyes are natural dyes that exclude the use of minerals or invertebrates in their production (eg. cadmium yellow is made from the minerals greenockite or hawleyite; carmine red or cochineal red is made from the cochineal scale insect; and royal purple is made from murex snails). The advantage to using vegetable dyes is that they’re (mostly) safe, renewable, and have minimal environmental impact because they are completely biodegradable when not coupled with inorganic mordants (dye fixers). While all color hues are possible through vegetable dyeing, many times more of it is necessary than is for synthetic dyes which makes it a costlier option. Additionally, vegetable dyes tend to be less colorfast than synthetics. While that is potentially a downside, some designers (such as Visvim) have used this quality to great effect through distressing, washing, or is accomplished by the user through wearing.
Notes On Some Specific Japanese Vegetable Dyes
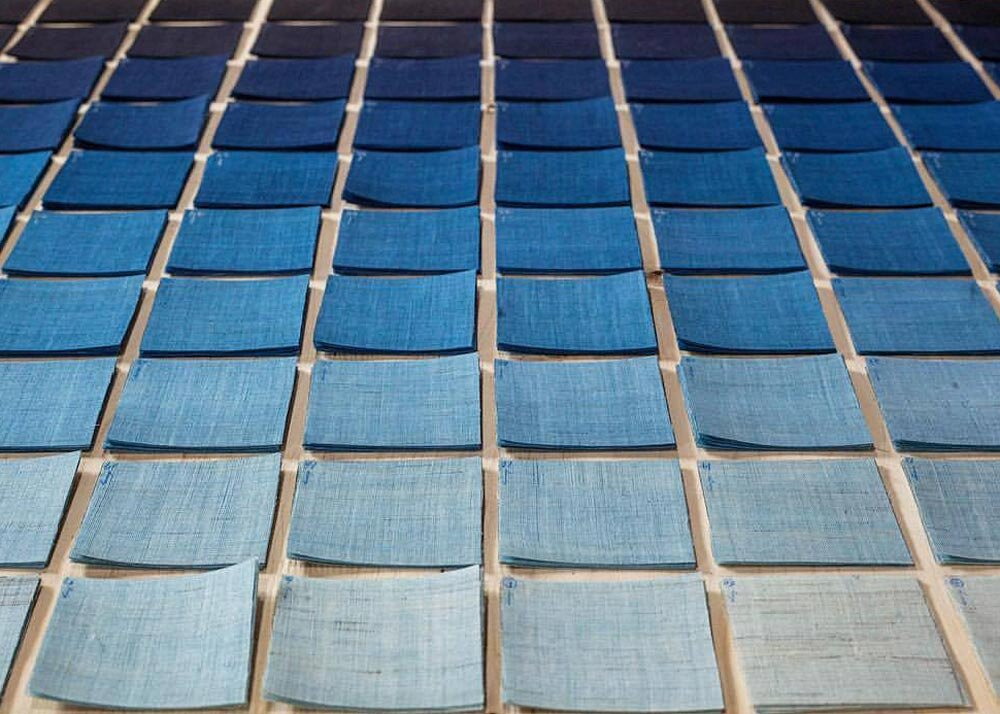
Shades of Japanese Indigo from Aijiro (the lightest shade) to Noukon (the darkest).
Indigo
To tackle the subject of indigo dyeing traditions would require its own exhaustive blog and the information is easily found on the internet, but I’ve included it here because there’s a couple of special notes as it relates to Japan:
Japanese indigo dyeing traditions date to the 10th century, but were popularized during the Edo Period (1603-1868). Known as ai-zome (or aizome) in Japan, the color’s depth and slow fade became the de facto uniform for the lower classes due to a prohibition on their wearing silk. As a matter of pride and status, indigo dyed clothing with white sashiko embroidery became a uniquely Japanese folk-art.
While American and European indigo is derived from Indigofera Tinctoria, most Japanese indigo is produced from Persicaria Tinctoria. There are many methods to extract the rich blue from the green leaves of the plant and nearly as many traditions as there are cultural regions in the world. In Japan, artisans developed a two step fermentation process that takes over a year from start to finish. From there, there are many possibilities and shades of blue that depend on the level of fermentation, the fiber used, and the dyeing time. The solution itself appears black, but once the fabric dries it takes on a unique shade of blue due to exposure to air. Depending on the number of dips, the color of the blue deepens, with each shade given a unique name. Aijiro indigo is the lightest shade closest to white, while noukon indigo is the darkest shade closest to black.
(For a tutorial on Indigo Dyeing with Yamato Indigo, click here.)
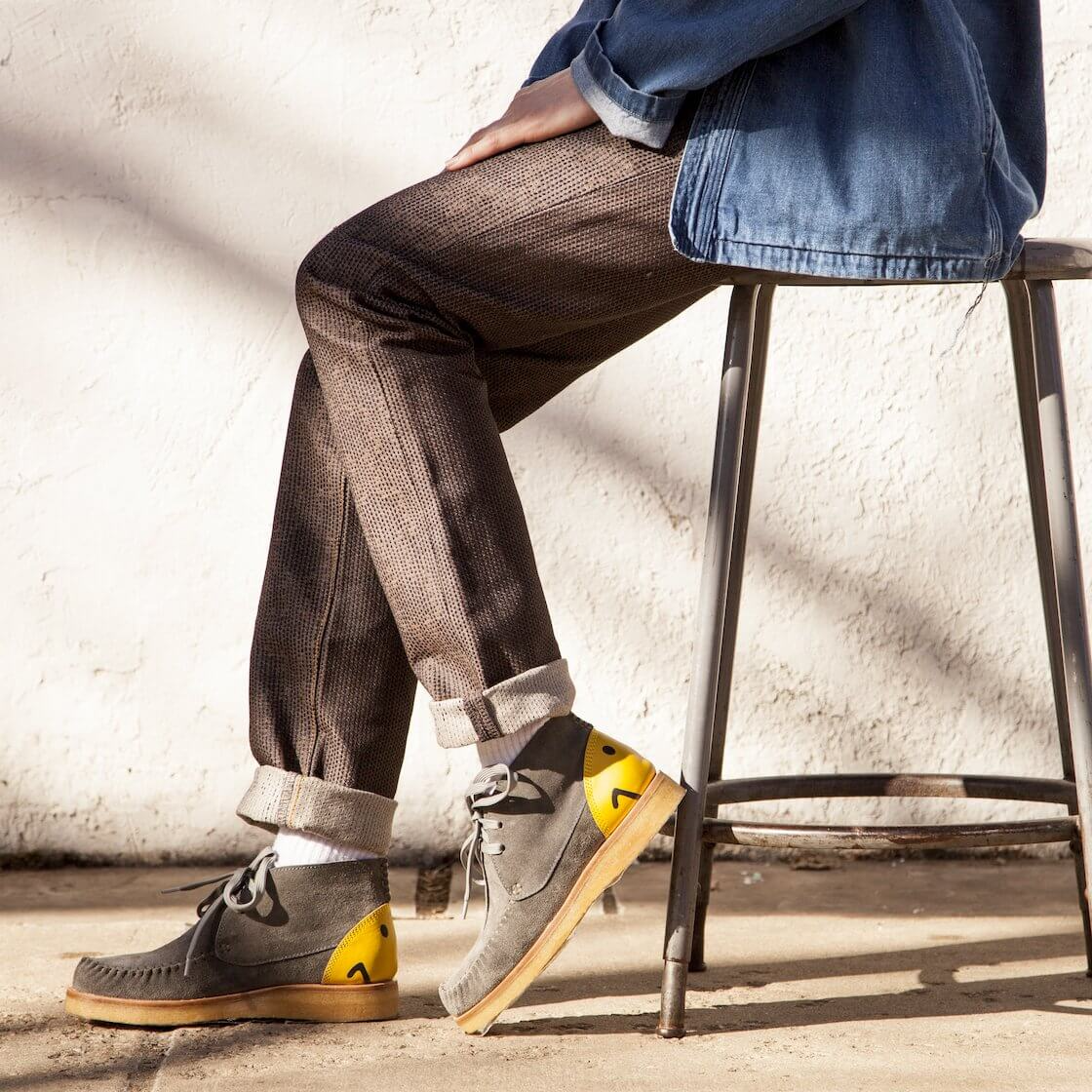
Kapital's Century Denim No. 5 utilizes Kakishibu dye derived from persimmons.
Persimmon or Kakishibu Dye
Dating back to the 13th century in Japan, kakishibu dye is made from unripe persimmons that have been fermented and aged for 2+ years. Kakishibu dye is a ruddy brown that fades to a brighter orange hue. Additionally, Kakishibu has been recognized as a great alternative to synthetic colors because it has many beneficial properties such as deterring insects, being naturally water-repellent, and having an anti-mold effect in cloth.
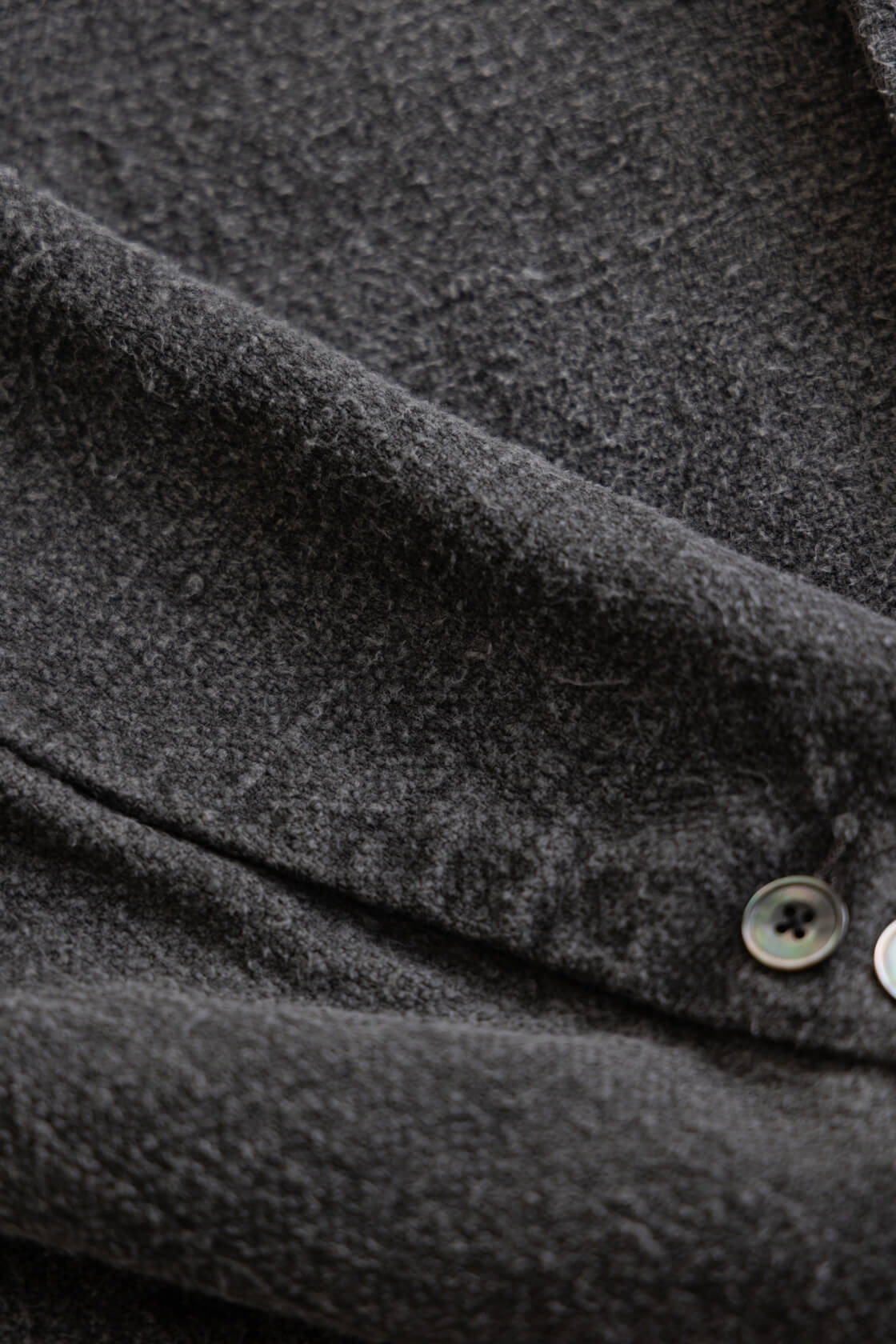
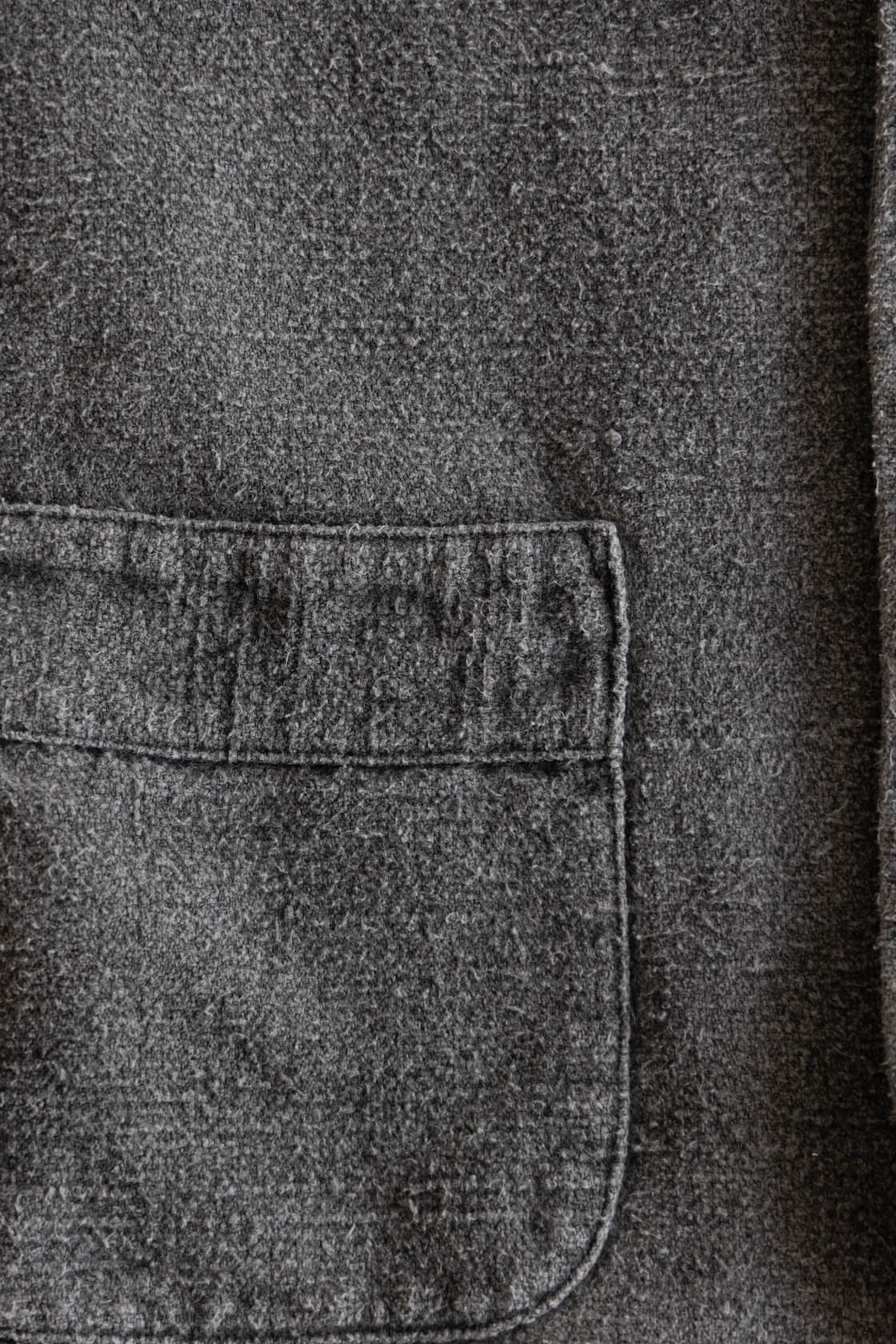
Sumi Dye
Another traditional Japanese dye more often used as a calligraphy ink, sumi is made from the turpentine soot of burned pinewood and produces tones from charcoal grey to black.
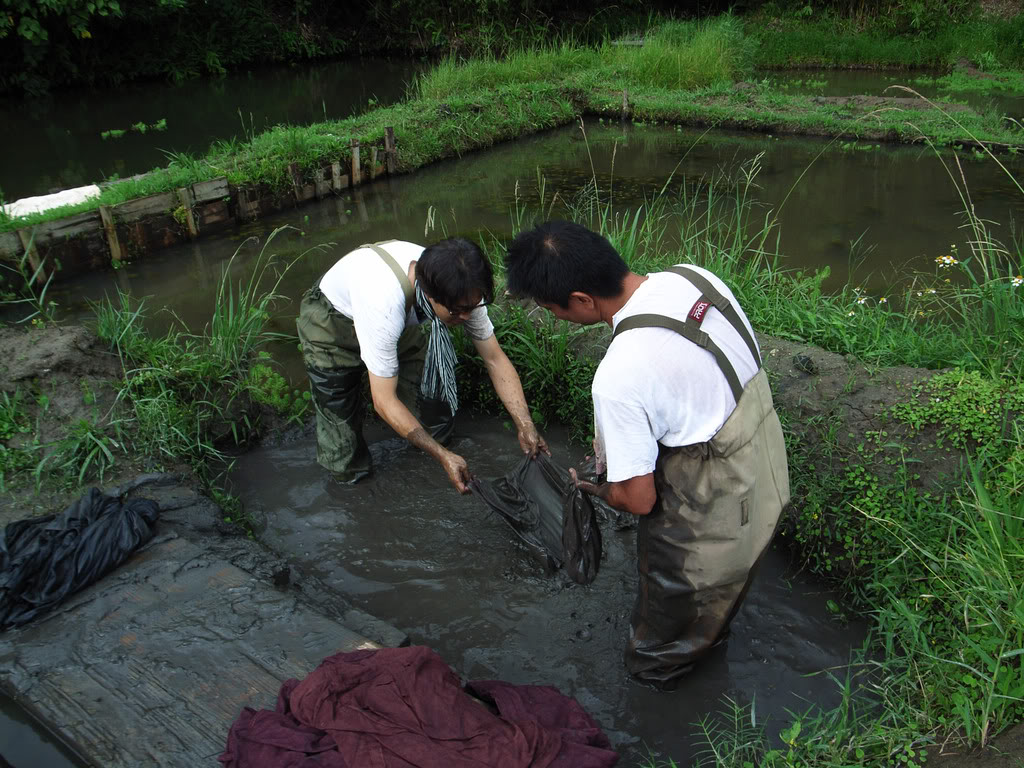
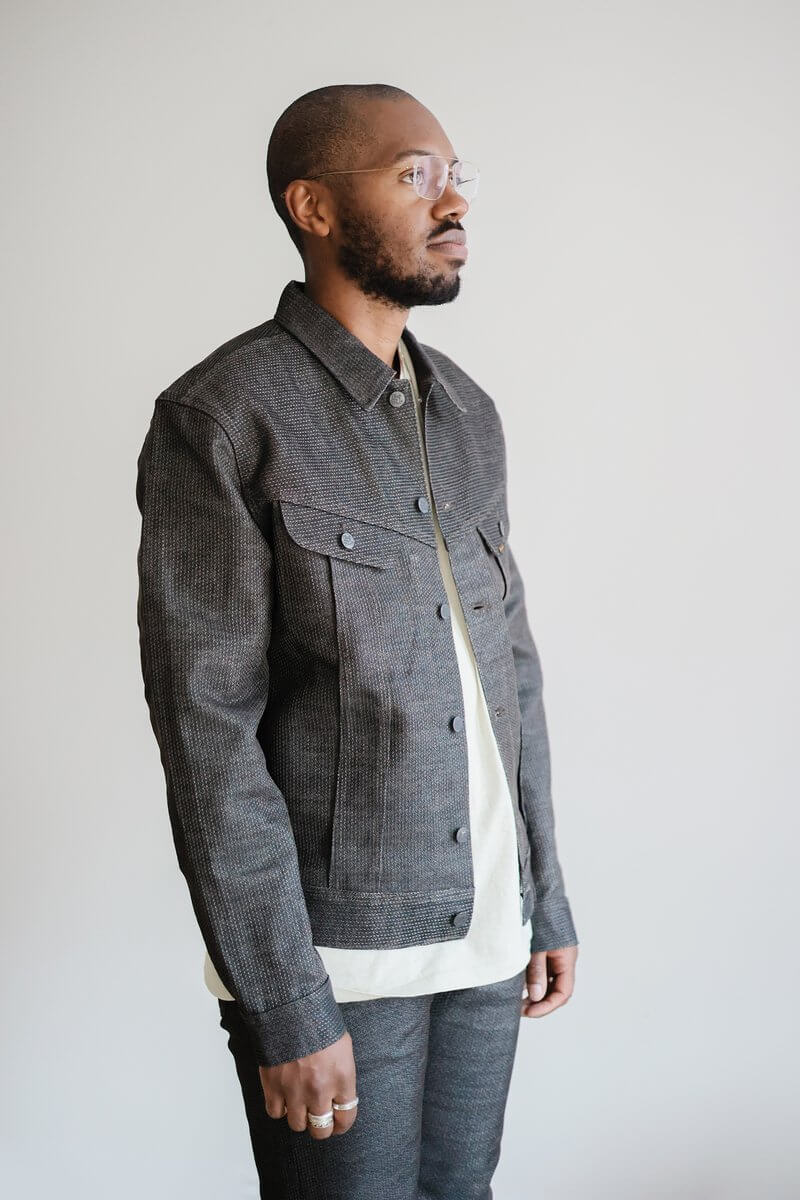
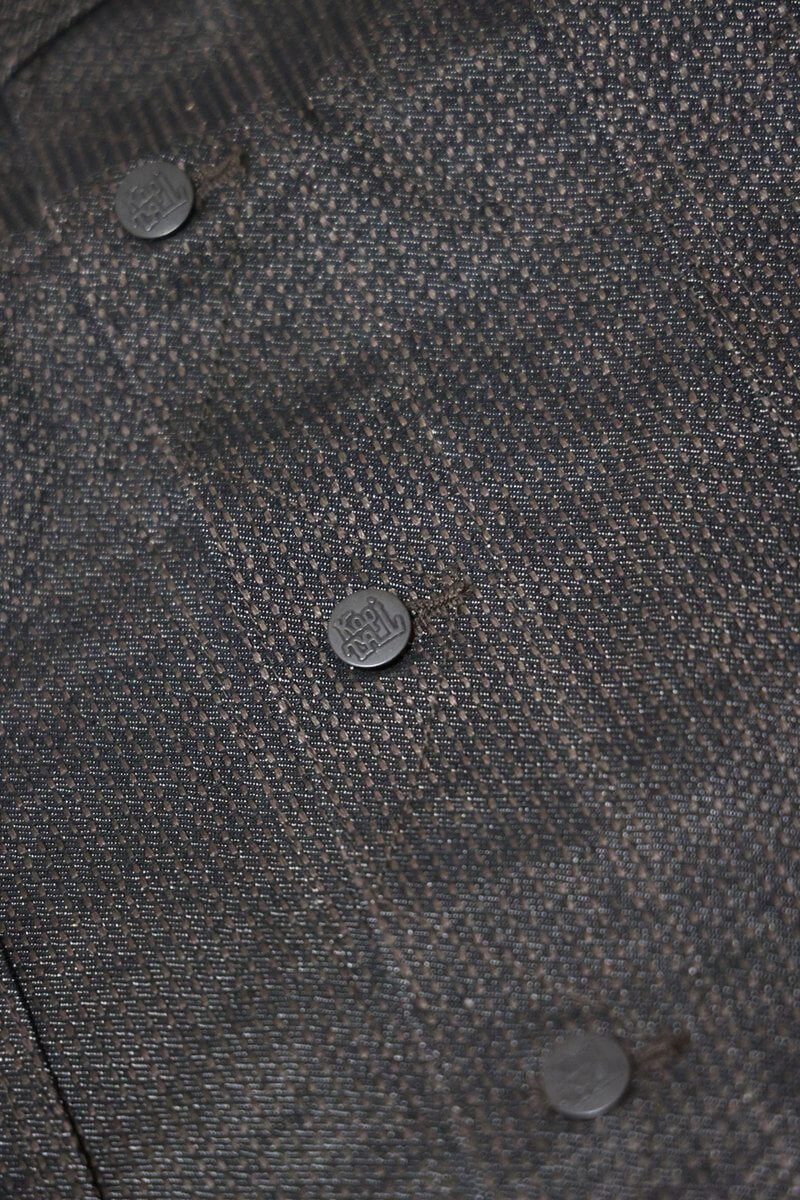
Top: The mud dyeing process. Bottom: Kapital's Century Denim No. 9 utilizes the initial dye coloration of the hawthorn in dorozome dye for the sashiko threads and the final grey/black dye is used in the base fabric.
Mud or Dorozome Dye
Mud-dyeing produces a rich and complicated grey. Unique to Japan’s Amami Oshima Island, mud dyeing is yet another traditional dyeing technique from the archipelego. The first step involves dyeing the garment with the bark of the Yeddo Hawthorn. The hawthorn chips, after being boiled, produces a rich mahogany color. After drying, it is then dyed in the mud of the island’s rice paddies. When the tannic acid found in the hawthorn encounters the strong iron content of the Amami Oshima mud, it undergoes a chemical reaction, turning the red fabric into a grey/black. Exemplary of this combination and process, Kapital keeps the initial dye coloration of the Hawthorn process for the sashiko stitches and dyes the base fabric in the grey/black of the mud dye in their Century Denim No. 9.
A Special Note on Dyeing Rayon and Other Synthetics
Synthetic textiles and rayon, which is semi-synthetic because it is most commonly produced using cellulose from reconstituted wood pulp, are generally produced in a melt spinning machine. (Liquid polymers are forced through holes in a plate to create strands that can then be used as yarns to be loomed into cloth. Here’s a video of a machine in production.) With rayon, the many types and grades effectively imitate the feel and texture of many natural fibers such as silk, wool, cotton, and linen. Due to their homogeneous chemical composition, rayon, synthetic fibers like polyester, and some acrylic-based fleeces, fully absorb dyestuffs. Whereas cotton is commonly dyed in the yarn that results in a colored thread with a white core (producing fades over time), synthetics mostly retain their color over time with the exception of chemical bleaching and some amount of minimal sun bleaching.
And that's that! Hopefully, every question on any esoteric industry term has been answered here, but feel encouraged to send us a note at secrethandshake@shopcanoeclub.com if you notice something missing.